Drive Systems in Electric Forklifts
Electric Heart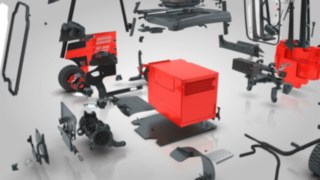
The electric engine is the economical and ecological alternative to the classic fuel cell. Its performance is determined by its energy-storage system. Over the decades various methods have been developed for making electricity available on the move. Lead-acid batteries, lithium-ion batteries and the fuel cell are among the key methods used for this.
Few doubt that the future of the engine will be electric. Electronic drive systems are often now not only the most cost-effective, but also the most ecologically sustainable option. This is a good thing as environmental sustainability is crucial in view of the climate crisis: in order to restrict global warming to two degrees Celsius, experts are demanding that the global economy be almost entirely decarbonized by the year 2050. The transport sector is considered to be the most problematic area here. With this in mind, the German federal government wants to put six million electric vehicles on the road by 2030. France and the UK are going even further and want to ban vehicles with combustion engines altogether by 2040. In the move towards electromobility, all eyes tend to be on the car of tomorrow. Industrial trucks’ crucial role in driving the electric revolution is often overlooked here. Delivery services and manufacturers of logistics vehicles are increasingly playing a pioneering role when it comes to electricity.
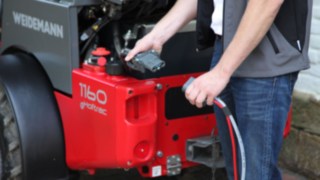
Sustainable pioneer: The electric farm loader from Weidemann is powered by lead-acid batteries from Linde.
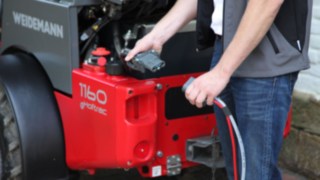
Sustainable pioneer: The electric farm loader from Weidemann is powered by lead-acid batteries from Linde.
Good for the Climate, Good for Business
It has been apparent for some time now that there is huge potential for climate protection in electric drive systems. How climate-friendly the electric engine is depends on how clean the electricity used is to produce. The greener the power, the better for the climate. In Germany, the proportion of energy generated by the sun, wind, water and biomass currently stands at around 40 percent. Under these conditions, the electric version already has a more favorable climate footprint than the combustion engine. If the green proportion of the electricity mix continues to grow as the energy revolution continues, the electric vehicle footprint will automatically improve.
Many companies can only benefit from the electric revolution from an economical point of view. Electric engines have a significantly lower servicing and maintenance requirement, which not only makes them clean but also a cheap alternative to the classic combustion engine.
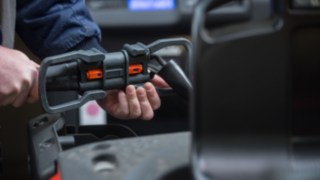
The Heart of a Truck
The performance of the electric drive is determined by its energy-storage system , the heart of the entire forklift. In recent decades, a wide range of options have been developed for conserving the electricity required. There are currently three main versions in use: the lead-acid battery, the lithium-ion battery and the fuel cell .
A Dominant Power: the Lead-Acid Battery
In 1854, German physicist Wilhelm Josef Sinsteden placed two large lead plates into a vessel containing diluted sulphuric acid. He quickly observed that this contraption could be used to store electricity from an external power source. Sinsteden developed the first functional lead-acid accumulator from his invention. Five years later, Frenchman Gaston Planté picked up the idea and improved it by arranging the lead plates in a spiral. In doing so, he established the fundamental principle on which batteries still work to this day.
Lead-acid batteries are now the most widely used storage batteries of all. At around 90 percent, they have by far the largest share of the worldwide battery market. They are used in almost all cars and motorbikes as starter batteries. As traction batteries, they are used to power e-bikes, forklift trucks, automatic transfer vehicles and electric specialty trucks.
This dominance is not for nothing. Lead-acid batteries are a highly robust, cost-effective type of battery with low maintenance costs, which can nonetheless deliver very high currents in a short period of time. They also demonstrate what is known as the memory effect, which means they hardly lose any charging capacity during their use. They can therefore be used to plan to a high degree of accuracy how much electricity can be saved at what cost. Another advantage of lead-acid batteries is their longevity: depending on quality and load, traction or storage batteries can last between five and 15 years.
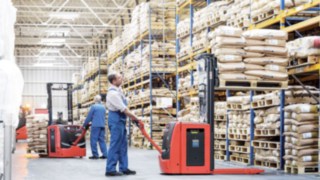
Powerful: the Lithium-Ion Battery
In 2019, John B. Goodenough, M. Stanley Whittingham and Akira Yoshino were awarded the Nobel Prize for Chemistry. Each of them made a crucial contribution to the development of lithium-ion batteries with their work. “The battery enabled the development of clean energy technologies and electric cars, which has led to a decrease in greenhouse gas emissions,” stated the Nobel committee in justifying the award.
Since its first appearance in the mid-1980s, the lithium-ion battery has gradually established itself in almost all areas of life. To begin with, it was mainly used to supply portable devices such as mobile phones, digital cameras and notebooks with power. It is now considered a crucial building block of modern electromobility. Li-ion batteries are small and light, yet still deliver a relatively large amount of energy. This makes them ideal for e-bikes, electric cars, modern electric wheelchairs and hybrid vehicles.
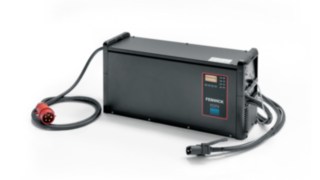
Lithium-ion batteries are especially safe as they do not emit dangerous gases.
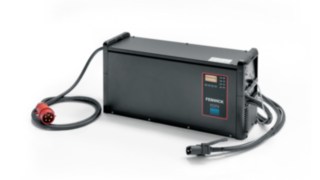
Lithium-ion batteries are especially safe as they do not emit dangerous gases.
Among experts, lithium-ion technology is currently considered the most effective and safest storage technology. While, for lead-acid batteries, it is recommended that they only be connected to the charger once they are fully discharged, interim charging is not only possible for lithium-ion batteries, it’s even the preferred method of charging. Their ideal charge level is between 20 and 80 percent of the overall capacity, which is why there is no danger of performance loss, even if the charge level is falling.
For industrial trucks such asforklift trucks and order pickers lithium-Ion batteries are also increasing in popularity. Their maintenance-free technology saves the company money, while the option of permanent interim charging significantly increases the vehicles’ availability. When cleaning the cells, there is no contamination due to battery gases or acids, which makes lithium-ion batteries useful for sensitive areas of work like the pharma or food industry.
Lightning Fast: the Fuel Cell
While the lithium-ion battery is undeniably the king of the current designs in the electrical sector, many are seeing the hydrogen fuel cell as the technology of the future. Fuel cells work similarly to batteries: a chemical reaction takes place inside them, whereby hydrogen reacts with oxygen thus generating electricity, heat and water vapor. This process is referred to as “cold combustion” and is especially environmentally friendly as no climate-damaging gases are produced. The hydrogen required can be produced using an electrolysis procedure. If this is done using electricity from renewable energies, the whole process is entirely CO2-neutral.
Unlike other electrical energy systems, fuel cells are not connected to a charging station, rather they are simply filled up with hydrogen. In terms of their practical handling, they resemble the conventional combustion engine. The cell can be filled in just three minutes and is ready for use again immediately. The fuel cell is particularly efficient when combined with a lithium-ion battery. In this hybrid drive, the fuel cell converts the hydrogen into electrical energy and uses it to drive the electric engine. This in turn charges the battery while driving. If a large amount of power is required, the battery assists as a backup storage system.
The fuel cell technology is already highly sophisticated. By 2030, according to estimates from theGerman Association of the Automotive Industryand theGerman Mechanical Engineering Industry Association, manufacturers will be in a position to bring greater quantities of hydrogen-powered private and commercial vehicles to market. The main missing factor preventing mass deployment for everyday transport is a developed filling station infrastructure.
In industry, however, demand is already rapidly increasing. By and large, companies are not reliant on a public network of filling stations for their logistics trucks. Just one hydrogen filling station on site is sufficient to refuel your entire fleet. There is therefore nothing standing in the way of day-to-day use in logistics, for example.